The role of three-dimensional printing technology in the medical field
Three-dimensional printing technology plays a vital and versatile role in the medical field, representing a revolutionary advancement in the design and manufacturing of medical devices and tissues. It allows doctors and surgeons to produce accurate models of internal structures of organs and blood vessels before surgery, contributing to improved diagnostic accuracy and surgical planning. In the field of dental prosthetics manufacturing, 3D printing allows for the creation of precise and customized dental prosthetics, reducing production time and enhancing the patient experience. Additionally, this technology is used to produce artificial body parts and customized prosthetics, providing an innovative solution for individuals who require tailored fittings that accurately match their physical structures. The integration of three-dimensional printing technology in the medical field enhances treatment capabilities, opening new horizons for innovation and delivering advanced and efficient healthcare.
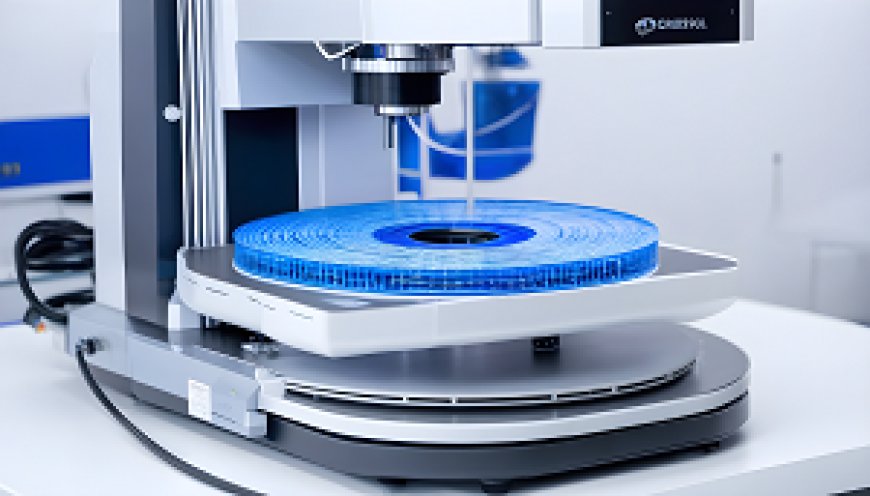
In the era of modern technology, 3D printing technology illuminates the medical field with innovation, enhancing our understanding and interaction with the profound advancements it has introduced in healthcare. This remarkable technology is not merely a manufacturing tool but serves as a platform empowering doctors and researchers to explore the frontiers of modern medicine. By employing 3D printing processes, accurate models of body organs and custom medical devices can be produced, opening new avenues for early diagnosis and treatment planning. This introduction serves as an exploration of the diverse and pioneering role that 3D printing technology plays in improving healthcare and facilitating progress in the field of medicine.
Applications of 3D Printing in Manufacturing Artificial Organs
The application of 3D printing in manufacturing artificial organs represents a significant advancement in the field of medical technology. The intricate and detailed nature of this process lends itself to a myriad of possibilities, addressing various challenges associated with traditional organ transplantation. The following are detailed aspects of the applications of 3D printing in the manufacturing of artificial organs:
1. Patient-Specific Customization
- One of the noteworthy applications of 3D printing in this context is the ability to create patient-specific and customized artificial organs. By utilizing medical imaging data, such as CT scans or MRI scans, 3D printing enables the fabrication of organs tailored to the unique anatomical features of individual patients. This level of customization enhances the compatibility of artificial organs, reducing the risk of rejection and improving overall transplant success rates.
2. Material Selection and Biocompatibility
- 3D printing allows for the precise selection of materials for manufacturing artificial organs. Biocompatible materials, such as bioinks and specialized polymers, can be used to create structures that closely mimic the mechanical and biological properties of natural organs. The ability to choose materials based on their compatibility with the human body is crucial for ensuring long-term functionality and minimizing adverse reactions.
3. Complex Geometries and Vasculature
- The intricate structures of human organs, including complex geometries and intricate vasculature, pose challenges for traditional manufacturing methods. 3D printing excels in overcoming these challenges by allowing for the layer-by-layer construction of organs with precise control over the internal and external features. This capability is particularly advantageous for replicating the complex vascular networks within organs, which is essential for proper functionality.
4. Prototyping and Iterative Design
- The iterative design process is a critical component in the development of artificial organs. 3D printing facilitates rapid prototyping, enabling researchers and clinicians to create multiple iterations of a design quickly. This iterative approach allows for fine-tuning and optimization of artificial organs, ensuring that the final product meets the required specifications for both form and function.
5. Tissue Engineering Integration
- In conjunction with 3D printing, advances in tissue engineering play a pivotal role in the manufacturing of artificial organs. By combining bioprinting techniques with 3D printing, it becomes possible to incorporate living cells and biomaterials into the printed structures. This integration promotes cellular proliferation, tissue regeneration, and overall organ functionality, bringing artificial organs closer to the complexity of their natural counterparts.
the applications of 3D printing in manufacturing artificial organs are multifaceted, ranging from patient-specific customization to the integration of advanced materials and tissue engineering techniques. This technology holds great promise in revolutionizing the field of organ transplantation, offering new possibilities for personalized and effective medical treatments.
The Role of 3D Printing in Crafting Custom Prosthetic Limbs
The role of 3D printing in crafting custom prosthetic limbs is a subject that delves into the intricacies of modern prosthetic technology, highlighting the advantages and nuances of employing additive manufacturing techniques in this specific domain. The process of creating custom prosthetic limbs through 3D printing involves a series of meticulous steps, each contributing to the overall precision and tailored functionality of the final prosthetic device.
1. Patient-Specific Measurements
- At the outset of the custom prosthetic limb fabrication process, precise measurements of the residual limb must be obtained. This involves employing advanced scanning technologies, such as laser scanning or structured light scanning, to capture detailed anatomical data. The collected data, including the dimensions and contours of the residual limb, serves as the foundation for the subsequent stages of prosthetic design.
2. Computer-Aided Design (CAD)
- Following the acquisition of patient-specific measurements, the data is translated into a digital format through computer-aided design (CAD) software. This digital representation allows prosthetists and designers to meticulously plan the structure and form of the prosthetic limb. The CAD model serves as a virtual blueprint, guiding the subsequent steps of the manufacturing process.
3. Additive Manufacturing Processes
- The core of the custom prosthetic limb manufacturing lies in the additive manufacturing processes facilitated by 3D printing. Utilizing various materials, such as thermoplastics or composite materials, layer-by-layer construction of the prosthetic limb is meticulously executed. This additive approach allows for the incorporation of intricate design features, ensuring a level of detail and customization that is challenging to achieve with traditional manufacturing methods.
4. Material Selection and Testing
- The choice of materials in 3D printing plays a crucial role in the functionality and durability of the prosthetic limb. Prosthetists carefully select materials based on factors such as strength, flexibility, and biocompatibility. Additionally, rigorous testing procedures are often employed to assess the mechanical properties of the printed materials, ensuring that the prosthetic limb meets the necessary standards for wear and tear, as well as comfort for the user.
5. Iterative Prototyping
- An inherent advantage of 3D printing in crafting custom prosthetic limbs is the ability to engage in iterative prototyping. This iterative process allows for the creation of multiple prototypes with minor adjustments, ensuring that the final prosthetic device aligns perfectly with the unique needs and preferences of the individual user. This iterative approach contributes to the overall user satisfaction and functionality of the prosthetic limb.
6. Incorporating Functional Components
- Beyond the structural elements, 3D printing enables the seamless integration of functional components into the prosthetic limb. This can include the incorporation of joints, hinges, or other mechanical features that mimic the natural movements of a human limb. The ability to customize and integrate such functional components enhances the overall user experience and functionality of the prosthetic limb.
the role of 3D printing in crafting custom prosthetic limbs is characterized by a methodical and detailed approach. From patient-specific measurements to additive manufacturing processes and iterative prototyping, each step contributes to the creation of prosthetic limbs that are not only tailored to individual needs but also showcase the potential of modern technology in enhancing the quality of life for amputees.
Enhancing Medical Diagnosis with 3D Organ Models
The integration of 3D organ models in medical diagnosis represents a meticulous and detail-oriented approach to augmenting the diagnostic process. This advanced technique involves the transformation of medical imaging data into three-dimensional representations, allowing for a comprehensive analysis of anatomical structures and potential pathological conditions.
1. Image Acquisition and Processing
- The initial step in enhancing medical diagnosis with 3D organ models involves the acquisition of medical imaging data. Modalities such as computed tomography (CT), magnetic resonance imaging (MRI), or ultrasound provide the foundational data sets. Subsequent to data acquisition, intricate processing algorithms are applied to convert the two-dimensional image slices into a three-dimensional format. This conversion process demands precision to ensure accurate anatomical representation.
2. Computer-Aided Segmentation
- To isolate specific organs or structures of interest, computer-aided segmentation techniques are employed. These algorithms meticulously identify and outline the boundaries of organs within the 3D image dataset. The segmentation process, although tedious, is crucial for creating accurate and detailed organ models, ensuring that the subsequent diagnostic analyses are based on precise anatomical information.
3. 3D Reconstruction and Visualization
- Following segmentation, the organ-specific data undergoes 3D reconstruction to generate detailed anatomical models. This process involves the creation of a volumetric representation that faithfully reproduces the spatial relationships of the organs. The resulting 3D models are then visualized using specialized software, allowing healthcare professionals to interact with and examine the organs from various angles and perspectives.
4. Pathological Simulation
- An important facet of enhancing medical diagnosis is the ability to simulate pathological conditions within the 3D organ models. By incorporating pathological data into the models, healthcare practitioners can visualize and analyze potential abnormalities or diseases affecting specific organs. This simulation capability aids in refining diagnostic accuracy and provides a comprehensive understanding of the potential clinical scenarios.
5. Surgical Planning and Education
- The 3D organ models find application not only in diagnosis but also in surgical planning. Surgeons can utilize these detailed models to plan and simulate complex surgical procedures. The ability to navigate and manipulate the 3D representations assists in strategizing surgical approaches, optimizing outcomes, and minimizing risks. Additionally, these models serve as valuable educational tools, offering a tangible and interactive learning experience for medical professionals.
6. Data Integration and Interdisciplinary Collaboration
- Enhancing medical diagnosis with 3D organ models involves integrating data from various sources, including medical imaging, patient records, and pathological information. This interdisciplinary approach fosters collaboration among healthcare professionals, ensuring a holistic understanding of the patient's condition. Radiologists, surgeons, and other specialists can collaboratively analyze the 3D models, contributing their unique perspectives to the diagnostic process.
the utilization of 3D organ models in medical diagnosis is characterized by a series of intricate steps, from image acquisition and segmentation to 3D reconstruction and visualization. The integration of these models into diagnostic workflows enhances the precision of anatomical analysis, facilitates pathological simulation, aids in surgical planning, and promotes interdisciplinary collaboration, ultimately contributing to more informed and accurate medical diagnoses.
The Impact of 3D Printing Technology on Surgical Tool Development
The impact of 3D printing technology on surgical tool development is a subject that warrants a comprehensive examination due to the multifaceted nature of its implications. This technological advancement has significantly transformed the landscape of surgical instruments, introducing a paradigm shift in their design, production, and utilization within the medical field.
- To begin with, the utilization of 3D printing technology in surgical tool development has ushered in a new era of customization and precision. Traditional manufacturing methods often involve subtractive processes, which can be limited in terms of intricate designs and personalized features. In contrast, 3D printing allows for the creation of complex, bespoke surgical tools that cater to the specific needs of individual patients or surgical procedures. This level of customization not only enhances the efficacy of the tools but also contributes to improved patient outcomes.
- Furthermore, the advent of 3D printing has streamlined the prototyping and iteration processes in surgical tool development. In the past, prototyping often involved time-consuming and costly procedures, with the potential for errors and delays. 3D printing mitigates these challenges by enabling rapid prototyping, allowing for the swift production of prototypes for evaluation and testing. This iterative approach facilitates the refinement of surgical tools, ensuring that they meet the stringent requirements of modern healthcare standards.
- Moreover, the materials used in 3D printing for surgical tools play a pivotal role in shaping their impact. The diversity of materials available for 3D printing allows for the creation of tools with varying degrees of strength, flexibility, and biocompatibility. This versatility ensures that surgical tools can be tailored to specific medical applications, ranging from orthopedic procedures to neurosurgery. The ability to choose materials with optimal characteristics enhances the functionality and durability of these instruments.
- In terms of cost-effectiveness, the integration of 3D printing technology in surgical tool development presents a compelling argument. While the initial investment in 3D printing equipment and materials may be substantial, the long-term benefits in terms of reduced production costs and waste make it an economically viable option. The ability to manufacture intricate designs with minimal material wastage contributes to sustainable and cost-efficient production processes.
- However, it is essential to acknowledge that the widespread adoption of 3D printing in surgical tool development is not without challenges. Quality control, standardization, and regulatory compliance are critical considerations that demand rigorous attention. The need for stringent validation processes to ensure the safety and efficacy of 3D-printed surgical tools is paramount, requiring collaboration between researchers, manufacturers, and regulatory bodies.
the impact of 3D printing technology on surgical tool development is profound and multifaceted. From customization and precision to rapid prototyping and material versatility, the advantages are evident. Nevertheless, the challenges associated with quality control and regulatory compliance underscore the importance of a meticulous and collaborative approach in harnessing the full potential of 3D printing in the realm of surgical tools. As technology continues to advance, it is poised to reshape the landscape of surgical procedures, offering unprecedented opportunities for innovation and improvement in patient care.
Utilizing 3D Printing in the Production of Dental Prosthetics
The purpose of this document is to delve into the intricate details surrounding the application of 3D printing technology in the production of dental prosthetics. As advancements in additive manufacturing continue to shape various industries, the dental field has not remained untouched. This exploration aims to provide an exhaustive overview of the processes, materials, and benefits associated with integrating 3D printing into the fabrication of dental prosthetic devices.
Materials and Processes
- The utilization of 3D printing technology in dental prosthetics involves a meticulous selection of materials and a step-by-step manufacturing process. Various biocompatible materials, such as resin-based polymers and ceramics, are meticulously chosen to ensure durability, functionality, and aesthetic appeal. The layer-by-layer additive manufacturing process is carefully orchestrated through computer-aided design (CAD) software, ensuring precise replication of the patient's oral anatomy.
Scanning and Digital Design
- A crucial facet of this methodology involves the acquisition of digital scans of the patient's oral cavity. Intraoral scanners capture detailed images, providing a digital blueprint for the prosthetic design. The digital data is then transferred to specialized software, where dental technicians meticulously design the prosthetic device. The CAD software enables fine-tuning of shapes, sizes, and contours to ensure a seamless fit and optimal functionality.
Layered Printing Process
- The 3D printing process is characterized by its layer-by-layer construction, where the chosen material is deposited in incremental layers based on the digital design. This additive manufacturing technique allows for precise control over the intricate details of the dental prosthetic, resulting in a customized and patient-specific end product. The layering process contributes to enhanced accuracy and reproducibility in comparison to traditional manufacturing methods.
Post-Processing and Finishing
- Following the completion of the 3D printing process, the dental prosthetic undergoes meticulous post-processing steps. This may involve the removal of support structures, surface smoothing, and polishing to achieve the desired level of aesthetics and comfort. Dental technicians employ various techniques, including manual finishing and polishing equipment, to ensure the final prosthetic meets the stringent quality standards required in dental applications.
Benefits and Considerations
- The integration of 3D printing in dental prosthetics offers a myriad of benefits, including improved accuracy, reduced production time, and enhanced customization. However, considerations such as material biocompatibility, regulatory compliance, and initial investment costs must be carefully evaluated by dental practitioners and laboratories adopting this technology.
the application of 3D printing technology in the production of dental prosthetics represents a paradigm shift in the field of dentistry. The combination of precise digital design, layered additive manufacturing, and meticulous post-processing results in customized prosthetic devices that align with the unique anatomical characteristics of each patient. This comprehensive exploration underscores the potential of 3D printing to revolutionize the dental prosthetics landscape, providing a foundation for further research and advancements in the intersection of dentistry and additive manufacturing.
3D Printing Technology for Generating Biofabricated Tissues for Transplants
The utilization of 3D printing technology in the realm of biofabrication for generating tissues earmarked for transplantation purposes is an area of burgeoning interest within the scientific community. This detailed exploration aims to elucidate the intricacies of how this technology is employed in the meticulous creation of biofabricated tissues, with a focus on its potential for enhancing the field of organ transplantation.
Material Selection and Composition
- One of the foundational aspects of employing 3D printing for biofabrication lies in the careful selection of biocompatible materials. These materials, often ranging from hydrogels to biodegradable polymers, play a pivotal role in ensuring that the resulting tissues not only possess the requisite mechanical properties but also exhibit compatibility with the human body, mitigating the risk of rejection post-transplant.
Digital Modeling and Design
- The process commences with the acquisition of precise medical imaging data, such as computed tomography (CT) scans or magnetic resonance imaging (MRI), which forms the basis for creating intricate digital models of the desired tissues. These digital blueprints serve as a virtual roadmap, guiding the subsequent 3D printing process to achieve a level of detail necessary for mimicking the complex microstructures inherent in natural tissues.
Layer-by-Layer Deposition
- A hallmark of 3D printing technology is its layer-by-layer deposition approach, wherein the selected biomaterials are intricately laid down in a predetermined pattern to construct the three-dimensional structure of the biofabricated tissue. This meticulous layering ensures the accurate reproduction of the tissue's architecture, facilitating the creation of constructs that closely resemble native tissues in terms of both form and function.
Bioprinting Techniques
- Within the realm of biofabrication, bioprinting techniques play a pivotal role. Various methods, including extrusion-based, inkjet-based, and laser-based bioprinting, are meticulously employed to deposit cell-laden bioinks onto the fabricated scaffolds. The choice of bioprinting technique is contingent upon factors such as cell type, viscosity of the bioink, and the desired tissue characteristics.
Cell Viability and Integration
- Ensuring the viability of cells within the biofabricated tissues is paramount for successful transplantation. The 3D printing process must strike a delicate balance between achieving structural integrity and preserving the vitality of encapsulated cells. Optimizing conditions for cell proliferation, differentiation, and integration into the surrounding tissue microenvironment is a critical aspect of the biofabrication process.
Challenges and Future Prospects
- Despite the promising strides made in the application of 3D printing technology for generating biofabricated tissues, challenges persist. Issues such as vascularization, immune response, and long-term functionality of the transplanted tissues remain focal points of ongoing research. As technology continues to advance, addressing these challenges holds the key to realizing the full potential of 3D printing in the realm of tissue transplantation.
the intersection of 3D printing technology and biofabrication presents a captivating frontier in the pursuit of generating tissues for transplantation. The nuanced interplay of material science, digital modeling, and bioprinting techniques underscores the complexity of this innovative approach. As research endeavors persist, the prospect of revolutionizing organ transplantation through the precision of 3D-printed biofabricated tissues beckons as a promising avenue for the future of regenerative medicine.
3D Printing Applications in Manufacturing Custom Medical Devices
3D printing, also known as additive manufacturing, has emerged as a revolutionary technology in various industries, including the field of manufacturing custom medical devices. This innovative process involves creating three-dimensional objects layer by layer from digital models, using materials such as plastics, metals, and ceramics. The applications of 3D printing in the manufacturing of custom medical devices have gained significant attention due to the technology's ability to provide precise and personalized solutions.
- One of the primary applications of 3D printing in the realm of custom medical devices is the production of patient-specific implants. This involves using medical imaging data, such as CT scans or MRI images, to create detailed digital models of a patient's anatomy. These digital models serve as the basis for designing and fabricating implants tailored to the individual patient's unique anatomical structure. The level of customization achieved through 3D printing allows for a more precise fit and better integration with the patient's body, reducing the risk of complications and improving overall patient outcomes.
- Furthermore, 3D printing is extensively used in the production of prosthetics and orthopedic devices. The ability to create complex, intricate structures with high precision makes 3D printing an ideal technology for manufacturing prosthetic limbs and orthopedic implants. Customization is a key advantage, as each device can be tailored to the specific needs and preferences of the individual patient. This personalized approach enhances the functionality and comfort of the devices, contributing to improved patient satisfaction and quality of life.
- In addition to patient-specific implants and prosthetics, 3D printing is also employed in the fabrication of surgical instruments. Surgeons can benefit from customized tools designed to match the specific requirements of a particular surgical procedure. This level of customization allows for the creation of instruments with intricate geometries and features that are not possible with traditional manufacturing methods. The result is improved surgical precision and efficiency, leading to better patient outcomes.
- The materials used in 3D printing for custom medical devices vary depending on the specific application. Biocompatible materials, such as medical-grade polymers and titanium alloys, are commonly employed to ensure that the printed devices are compatible with the human body. The careful selection of materials is crucial to meet regulatory standards and ensure the safety and effectiveness of the medical devices.
- Despite the numerous advantages of 3D printing in manufacturing custom medical devices, challenges still exist. Issues such as material compatibility, post-processing requirements, and regulatory compliance need to be carefully addressed to ensure the reliability and safety of the printed devices. Moreover, the cost of 3D printing technology and materials can be a limiting factor, although ongoing advancements in the field are gradually mitigating this concern.
3D printing has become an indispensable technology in the manufacturing of custom medical devices, offering unparalleled levels of precision and customization. From patient-specific implants to prosthetics and surgical instruments, the applications of 3D printing in the medical field continue to evolve, paving the way for a new era of personalized healthcare. As the technology matures and further innovations emerge, it is likely that 3D printing will play an increasingly significant role in shaping the future of medical device manufacturing.
Harnessing 3D Printing for Surgical Training Purposes
The utilization of three-dimensional (3D) printing technology in the field of surgical training has emerged as a subject of considerable interest and significance. This innovative approach aims to revolutionize the conventional methods of surgical skill acquisition by leveraging the capabilities of 3D printing to produce anatomically accurate models.
Background
- The backdrop of this exploration involves a comprehensive understanding of the historical evolution of surgical training methodologies. Traditionally, surgeons-in-training have relied on cadaveric dissections and two-dimensional illustrations to grasp the complexities of human anatomy. The advent of 3D printing technology has, however, ushered in a new era, promising enhanced realism and tactile experiences in the realm of surgical education.
Materials and Techniques
- One fundamental aspect of harnessing 3D printing for surgical training involves an examination of the materials and techniques employed in the fabrication of anatomical models. Various biocompatible materials, such as thermoplastics and photopolymers, are meticulously deposited layer by layer, guided by detailed digital renderings derived from medical imaging data. The precision of these printing processes ensures a faithful reproduction of anatomical structures, enabling surgeons to practice and refine their skills on lifelike replicas.
Customization and Patient-Specific Models
- A noteworthy dimension of 3D printing in surgical training pertains to the customization and generation of patient-specific anatomical models. By utilizing patient-specific medical imaging data, such as CT scans and MRIs, surgeons can replicate the unique anatomical features of individual patients. This personalized approach allows for targeted training scenarios, enabling surgeons to rehearse specific procedures tailored to the nuances of a patient's anatomy.
Simulation-Based Learning
- The integration of 3D-printed anatomical models into surgical training programs facilitates simulation-based learning. Surgeons-in-training can engage in hands-on practice, honing their skills in a risk-free environment before transitioning to live patient cases. The tactile feedback provided by these models enhances the sensory experience, contributing to the development of muscle memory and spatial awareness crucial in surgical procedures.
Educational Impact
- Examining the educational impact of incorporating 3D printing into surgical training programs involves an assessment of the perceived benefits and potential drawbacks. While the technology offers unparalleled advantages in terms of realism and customization, challenges such as cost, accessibility, and the need for ongoing updates to reflect evolving medical knowledge must be carefully considered.
the harnessing of 3D printing for surgical training purposes represents a transformative stride in the evolution of surgical education. The precision, customization, and simulation capabilities offered by this technology hold the promise of revolutionizing the way surgeons acquire and refine their skills. As the field continues to advance, it is imperative to address challenges and ensure the seamless integration of 3D printing into mainstream surgical training curricula.
3D Printing in Producing Anatomical Models for Medical Education
The integration of 3D printing technology in the realm of medical education has garnered significant attention due to its potential to revolutionize the traditional methods of teaching anatomy. This paper meticulously examines the intricate details of how 3D printing is employed in the creation of anatomical models for medical education, emphasizing its applications, benefits, and challenges.
Methods
- The production process of 3D anatomical models involves several steps, each requiring meticulous attention to detail. Initially, a high-resolution digital model of the anatomical structure is created using advanced imaging techniques such as computed tomography (CT) or magnetic resonance imaging (MRI). Subsequently, the digital model undergoes segmentation, wherein the anatomical structure is divided into distinct regions, facilitating precise reproduction through 3D printing.
Printing Materials and Technologies
- The choice of printing material is paramount in achieving anatomical accuracy. Commonly utilized materials include thermoplastics, photopolymers, and bioinks. Different printing technologies, such as fused deposition modeling (FDM), stereolithography (SLA), and selective laser sintering (SLS), each come with their own set of advantages and limitations, further complicating the decision-making process for educators and model producers.
Applications in Medical Education
- The versatility of 3D printing in medical education is vast. Anatomical models, generated with exceptional precision, serve as invaluable tools for teaching complex anatomical structures and spatial relationships. Furthermore, these models offer a hands-on experience for medical students, enhancing their understanding and retention of anatomical knowledge. The use of 3D-printed models is not limited to academic settings; they find application in surgical planning, patient communication, and research.
Benefits and Challenges
- While the benefits of 3D printing in medical education are evident, including enhanced visualization and improved tactile learning experiences, challenges persist. Issues such as cost, time, and the need for skilled personnel in 3D model creation and printing hinder widespread adoption. Additionally, ensuring the biological accuracy of printed models remains a constant challenge, demanding continuous refinement in printing technologies and materials.
the integration of 3D printing in the production of anatomical models for medical education is a topic of extensive exploration. This comprehensive examination underscores the meticulous processes involved, the various materials and technologies employed, and the multifaceted applications in medical education. As the technology continues to advance, addressing the existing challenges will be crucial in realizing the full potential of 3D printing for anatomical education in the medical field.
Improving Communication Among Medical Teams Through 3D Models
This document aims to provide an in-depth analysis of the strategies employed for improving communication within medical teams through the integration of 3D models. Effective communication among healthcare professionals is crucial for ensuring comprehensive patient care. The utilization of 3D models presents a potential avenue to enhance the clarity and precision of information exchange among medical team members, contributing to more informed decision-making processes.
Integration of 3D Models in Medical Communication
- One noteworthy aspect of recent efforts to enhance communication within medical teams involves the incorporation of 3D models into the collaborative framework. These models, generated through advanced imaging techniques and 3D printing technologies, offer a tangible and visual representation of complex anatomical structures. By facilitating a shared understanding of patient-specific conditions, medical teams can potentially reduce misinterpretations and enhance the accuracy of diagnostic discussions.
Multidisciplinary Collaboration
- The implementation of 3D models fosters multidisciplinary collaboration among various medical specialties. Radiologists, surgeons, and other healthcare professionals can benefit from a common visual reference point, allowing for more effective discussions about treatment plans and surgical interventions. The interdisciplinary nature of healthcare necessitates clear and concise communication, and 3D models provide a tangible platform for cross-specialty understanding.
Preoperative Planning and Visualization
- One area where 3D models have demonstrated significant potential is in preoperative planning and visualization. Surgeons can utilize patient-specific 3D models to meticulously plan surgical procedures, foresee potential challenges, and strategize for optimal outcomes. The visual representation offered by these models aids in conveying complex surgical plans to the entire medical team, aligning all members with a unified understanding of the intended approach.
Enhanced Patient Education
- In addition to facilitating communication within the medical team, 3D models contribute to enhanced patient education. Visual aids, such as 3D-printed anatomical replicas, empower healthcare providers to convey complex medical information to patients in a more accessible manner. This can lead to improved patient understanding, increased engagement in treatment decisions, and ultimately better patient outcomes.
Challenges and Considerations
- Despite the potential benefits, the integration of 3D models in medical communication is not without challenges. Issues such as standardization of 3D printing processes, accessibility of technology, and the need for training among healthcare professionals pose considerations for widespread implementation. Additionally, the financial implications of adopting such technologies and the time required for model generation and review must be carefully weighed.
the incorporation of 3D models represents a promising approach to improving communication among medical teams. From enhancing interdisciplinary collaboration to aiding in preoperative planning and patient education, 3D models contribute to a more comprehensive and cohesive healthcare ecosystem. However, careful consideration of challenges and the development of standardized practices are essential to fully harness the potential benefits of this innovative communication tool within the medical field. This exploration provides a detailed overview of the role of 3D models in enhancing medical communication, emphasizing the need for ongoing research and collaboration in this dynamic domain.
Advancements in 3D Printing Technology for Medical Research and Innovation.
This document seeks to comprehensively analyze the recent advancements in 3D printing technology as applied to the realm of medical research and innovation. In the ever-evolving landscape of healthcare, the integration of 3D printing has emerged as a noteworthy avenue for pushing the boundaries of medical science. This exploration aims to elucidate the intricate details surrounding the utilization of 3D printing in medical research, highlighting its potential contributions to innovation and progress within the field.
Materials and Techniques
- Advancements in 3D printing for medical research involve a meticulous selection of materials and sophisticated printing techniques. Biocompatible materials, ranging from polymers to metals, are scrutinized for their suitability in replicating complex anatomical structures. The printing techniques themselves are characterized by layer-by-layer additive manufacturing, guided by computer-aided design (CAD) models. This methodical approach ensures precision and accuracy in the replication of medical models and prototypes.
Patient-Specific Models
- One noteworthy aspect of the recent progress in 3D printing technology lies in its ability to generate patient-specific models for medical research and preoperative planning. The integration of medical imaging, such as CT scans or MRI data, facilitates the creation of anatomically accurate models. These patient-specific models offer researchers and medical professionals an invaluable tool for visualizing complex structures, enhancing surgical planning, and improving overall procedural outcomes.
Complex Organ Printing
- Recent strides in 3D printing have led to ambitious endeavors in the field of complex organ printing. Researchers are exploring the feasibility of printing functional organs, such as hearts and kidneys, using a combination of biological and synthetic materials. This groundbreaking avenue of research holds promise for addressing the global shortage of organ donors, although substantial challenges remain in achieving the necessary vascularization and cellular integration for viable organ functionality.
Bioprinting and Tissue Engineering
- The convergence of 3D printing with bioprinting techniques has opened new frontiers in tissue engineering. This involves the layer-by-layer deposition of biological materials to create three-dimensional structures that mimic natural tissues. The precision afforded by 3D printing in this context enables the fabrication of intricate tissue scaffolds, fostering advancements in regenerative medicine and the potential for organ transplantation.
Challenges and Considerations
- Despite the promising strides in 3D printing for medical research, several challenges and considerations persist. Issues such as regulatory approvals, standardization of processes, and the need for extensive validation studies pose hurdles to the widespread adoption of these technologies. Furthermore, ethical considerations surrounding the use of 3D printing in medical research, particularly in the context of organ printing and bioprinting, necessitate careful scrutiny and ethical frameworks.
the recent advancements in 3D printing technology herald a new era in medical research and innovation. From patient-specific models to the ambitious pursuit of printing complex organs, 3D printing has the potential to revolutionize how medical professionals approach research, diagnosis, and treatment. However, the road ahead is not without challenges, and a judicious balance between innovation and ethical considerations must be maintained as the healthcare community navigates this exciting frontier. This exploration serves as a detailed overview of the recent progress in 3D printing for medical research, emphasizing its transformative potential and the need for ongoing research and collaboration in this dynamic field.
In conclusion
3D printing technology stands out as a vital and central axis in the revolutionary transformation witnessed in the fields of healthcare and medicine. Thanks to its ability to produce accurate models of human organs and manufacture specialized medical devices, this technology promotes innovation in disease diagnosis and treatment plans, contributing to the improvement of healthcare quality and the acceleration of recovery processes. 3D printing can be seen as a driver for progress in medical training, surgical tool development, and providing customized solutions for patients in areas such as artificial limb manufacturing and tissue regeneration. This diverse and advanced role of 3D printing technology opens up limitless opportunities to make significant strides in the medical journey, with boundless potential to enhance healthcare and achieve astonishing medical innovations.
What's Your Reaction?
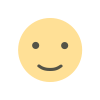
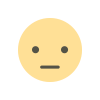
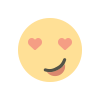
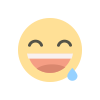

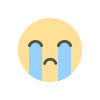
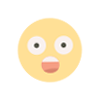